Nghiên cứu chế tạo lớp phủ kép chống ăn mòn từ hợp kim Crom - Niken và Nhôm
Thứ ba, 08/07/2025 - 08:43
Lớp phủ nhôm và phủ hợp kim CrNi với những ưu điểm riêng nổi trội như nhẹ, bảo vệ theo cơ chế anode, chống ăn mòn cao. Do đó, hệ vật liệu phủ tổ hợp CrNi và nhôm tổ hợp các hiệu ứng trên, góp phần nâng cao tuổi thọ làm việc của các kết cấu nền.
Tóm tắt:
Trong nghiên cứu này sử dụng lớp phủ kép Cr-Ni và Al vừa có tác dụng rào cản chống lại sự xâm nhập của tác nhân ăn mòn, đồng thời lại có tính năng hoạt động của anode bảo vệ nền thép ngay cả khi nền thép bị hở. Kết quả xác định tính chất cơ lý hóa của lớp phủ cho thấy độ bám dính của lớp phủ Cr-Ni trên nền thép khoảng 30,14 Mpa cao hơn độ bám dính của lớp phủ nhôm trên nền thép nên việc sử dụng lớp phủ Cr-Ni ở dưới có tác dụng tăng độ bám dính so với lớp phủ nhôm trực tiếp trên nền thép. Nghiên cứu điện hóa, đánh giá khả năng bảo vệ chống ăn mòn của lớp phủ trong acid HCl cho thấy hệ lớp phủ bền ở pH 5, 6. Hình ảnh SEM trước và sau khi thử ăn mòn cho thấy sự ổn định của lớp phủ ở pH 5, 6.
Từ khóa: ăn mòn acid, ăn mòn, lớp phủ.
1. Tổng quan
Trong điều kiện làm việc của nhà máy, đặc biệt các nhà máy hoạt động trong lĩnh vực công nghiệp nặng, môi trường acid thường dẫn đến việc phá hỏng hàng loạt các chi tiết máy bằng vật liệu kim loại. Khi sử dụng hợp kim có độ bền cao để nâng cao tuổi thọ của chi tiết máy giá thành thường quá cao. Vì vậy cách giải quyết tốt nhất là tạo một lớp phủ kim loại trên nền thép thông dụng. Lớp phủ nhôm và phủ hợp kim CrNi với những ưu điểm riêng nổi trội như nhẹ, bảo vệ theo cơ chế anode, chống ăn mòn cao. Do đó, hệ vật liệu phủ tổ hợp CrNi và nhôm tổ hợp các hiệu ứng trên, góp phần nâng cao tuổi thọ làm việc của các kết cấu nền.
2. Thực nghiệm
2.1. Hóa chất
Hạt mài Al2O3 (coranhdong), kích thước hạt (0,8 - 1,2) mm; dung môi aceton (Đài Loan); dây hợp kim Cr20Ni80; Acid HCl 30 - 33%.
2.2. Chế tạo lớp phủ bằng công nghệ phun phủ hồ quang điện
Quy trình chế tạo lớp phủ bằng công nghệ phun phủ hồ quang điện được mô tả trong Hình 1. Đầu tiên mẫu được làm sạch bằng vải sạch tẩm dung môi aceton, sau đó nhúng vào nước sạch để bề mặt được khử nốt các chất bẩn còn lại, sau đó sấy khô. Làm sạch và tạo nhám bề mặt mẫu bằng cách phun hạt mài Al2O3. Mẫu sau khi làm sạch cần tiến hành phun kim loại chậm nhất là 2 giờ để tránh việc mẫu sau khi làm sạch bị oxi hóa trở lại. (Hình 1)
Hình 1: Quy trình công nghệ chuẩn bị bề mặt
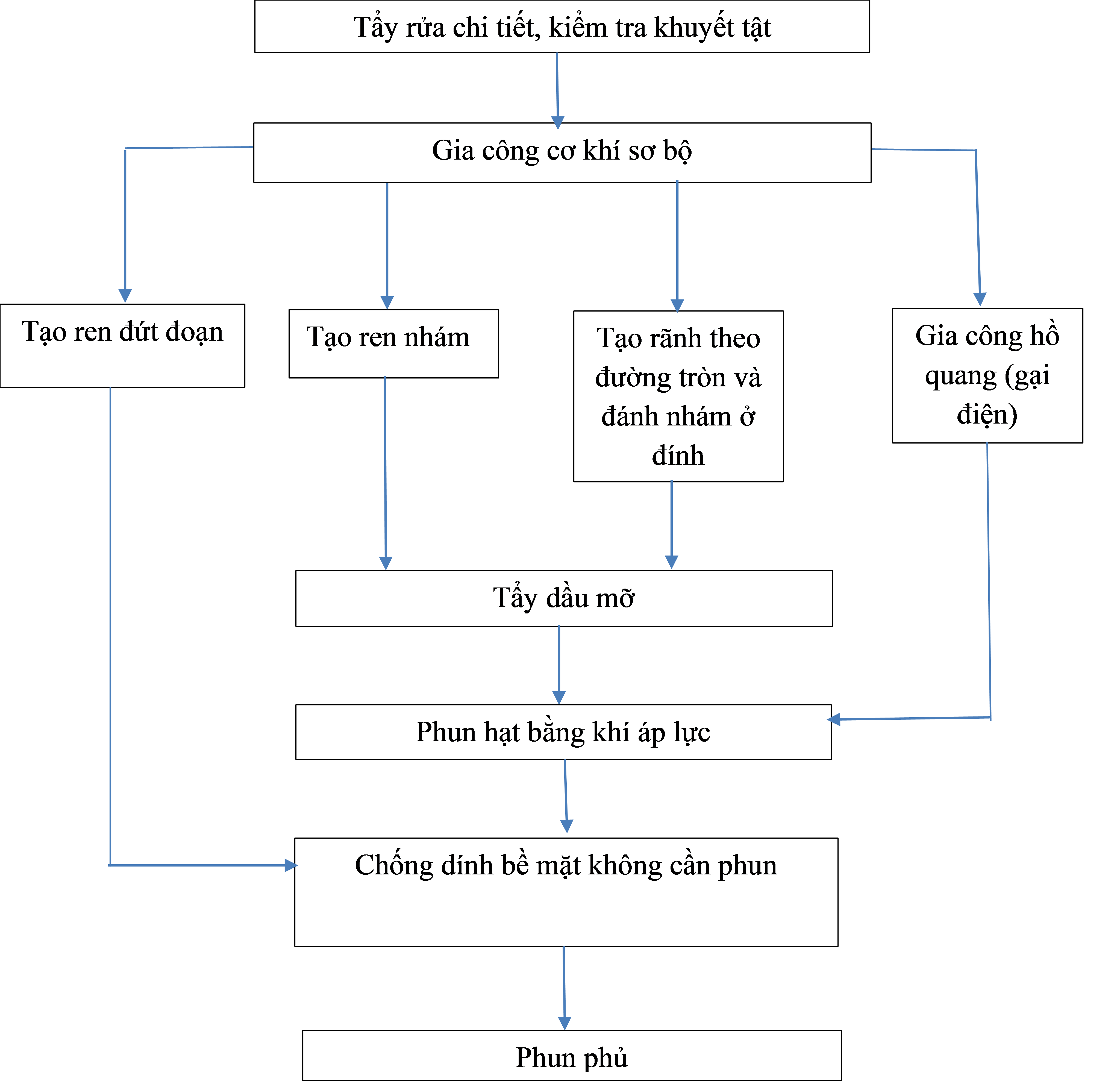
Chọn vật liệu phủ và tạo lớp phủ: sử dụng hai loại vật liệu là dây Cr20Ni80 và dây Al. Dây nhôm có độ tinh khiết cao với độ sạch đạt hơn 99,5%. Thành phần hóa học cơ bản của loại dây Cr20Ni80 được trình bày như bảng 1.
Loại dây | C (%) | Cr (%) | Ni (%) | Ti (%) | Si (%) | Mn (%) | Fe (%) |
Cr20Ni80 | < 0,15 | 22 - 23 | 75 - 78 | - | - | - | - |
Bảng 1. Thành phần hóa học cơ bản của dây hợp kim Cr20Ni80
Sử dụng thiết bị phun hồ quang điện với đầu dây LD/U-2, đường kính dây 3,5 mm, tốc độ cấp dây 0,35 m/s tương ứng với năng suất phun khoảng 120 kg/giờ. Thông số công nghệ thực hiện với các chế độ phun được thực hiện như bảng 2.
STT | Chế độ | Thông số |
1 | Góc phun (o) | 90 |
2 | Khoảng cách phun (mm) | 100 - 200 |
3 | (atm) | 4 - 6 |
4 | Điện áp hồ quang (V) | 21,3 - 25,7 |
5 | Cường độ dòng điện (A) | 150 |
6 | Vận tốc di chuyển đầu phum (mm/s) | 20 |
7 | Kỹ thuật phun | Kỹ thuật phun thẳng |
Bảng 2. Chế độ phun cho loại dây Cr20Ni80
Mẫu đo độ bám dính lớp phủ được chế tạo dùng để kiểm tra độ bám dính lớp phủ trên nền theo tiểu chuẩn châu Âu NE 582: 1993 có hình dạng và kích thước như Hình 2.
Hình 2: Kích thước mẫu đo độ bám dính lớp phủ
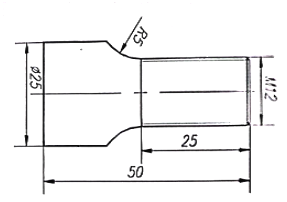
Chuẩn bị mẫu thử ăn mòn: Khoan 1 lỗ ở góc mẫu, cách rìa mỗi phía 2 mm để hàn dây dẫn điện. Hàn dây dẫn điện để thực hiện các phép đo ăn mòn điện hóa. Đổ nhựa cách ly bề mặt lớp phủ bằng nhựa epoxy không thấm nước, chịu acid với độ dày (3 - 5) mm.
Mẫu sau khi thử ăn mòn được tiếp tục mài thô, mài phẳng trên giấy ráp với cỡ hạt lớn đến nhỏ (150 - 2000) và đánh bóng. Các mẫu mày được mang đi quan sát và chụp ảnh tổ chức tế vi bằng máy hiển vi điện tử quét JSM 5410 - JEOL Japan.
2.3. Đánh giá khả năng bảo vệ chống ăn mòn của lớp phủ
2.3.1. Xác định tính chất cơ, lý của lớp phủ
- Khoan lỗ, buộc chỉ tạo dây treo sau đó đem sấy khô trong lò sấy ở 80oC trong 8 giờ.
- Đem cân khô
- Nhúng parafin để tạo lớp ngăn cách không thấm nước rồi đem cân khô.
- Đem cân trong nước.
2.3.2. Đo điện hóa
Việc đầu tiên trước khi đo là kiểm tra lại điện cực chuẩn: ống thủy tinh của điện cực chuẩn cần lấp đầy bằng dung dịch KCl bão hòa. Ta dùng ba điện cực: điện cực làm việc là mẫu cần đo, điện cực đối Ti, điện cực chuẩn là điện cực calomel bão hòa.
Quét đường cong phân cực xác định RP và Ecorr
Đo tổng trở điện hóa bằng cách sử dụng tín hiệu dòng xoay chiều hình sin với tần số f tử 106 đến 10-2 Hz, biên độ dao động ∆E = 5mL. Xác định giá trị điện thế mạch hở OCP chờ trong 30s để dòng ổn định, ghi lại giá trị điện thế.
3. Kết quả và thảo luận
TT | Lực kéo đứt | Độ bền kéo (MPa) |
1 | 5424,93 | 22,11 |
2 | 15617,52 | 31,83 |
3 | 1789,33 | 36,47 |
Trung bình | 30,14 |
Độ bám dính lớp phủ hợp kim CrNi trên nền thép cao hơn độ bám dính của lớp phủ Al trên nền thép (15,27 MPa). Như vậy, việc sử dụng lớp phủ hợp kim CrNi ở dưới lớp phủ nhôm có tác dụng tăng độ bám dính so với lớp phủ nhôm trực tiếp trên nền thép.
Quan sát bề mặt lớp phủ sau 168 giờ cho thấy trong dung dịch HCl và dung dịch HNO3 ở pH 4, 5, 6 lớp phủ gần như còn nguyên vẹn và xuất hiện những lớp thụ động màu trắc trên bề mặt (phần bề mặt có sản phẩm ăn mòn không tan - lớp thụ động).
Tiến hành quét đường cong phân cực theo thời gian tại các thời điểm sau khi ngâm mẫu là 0,5 giờ; 3 giờ; 168 giờ; 336 giờ; 672 giờ; 840 giờ... thu được các giá trị điện thế ăn mòn Ecorr và Rp. Dựa vào số liệu, ta vẽ được đồ thị biểu diễn sự biến thiên của Rp và Ecorr theo thời gian đối với lớp phủ kép trong dung dịch HCl pH 4 (Hình 3 và Hình 4).
Hình 3: Biến thiên Ecorr theo thời gian đối với hệ phủ kép trong dung dịch HCl pH 4
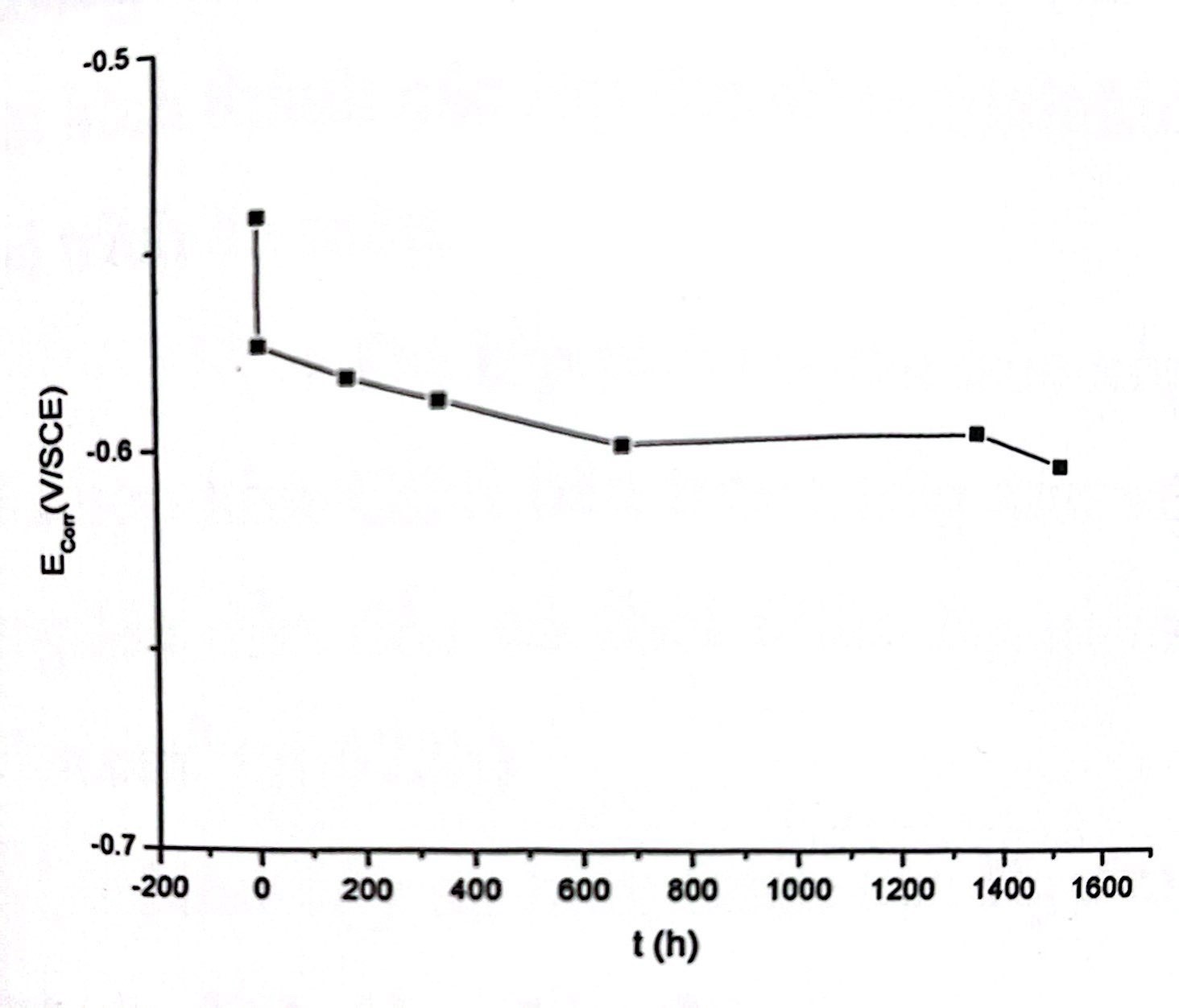
Hình 4: Biến thiên Rp theo thời gian trong dung dịch HCl pH 4
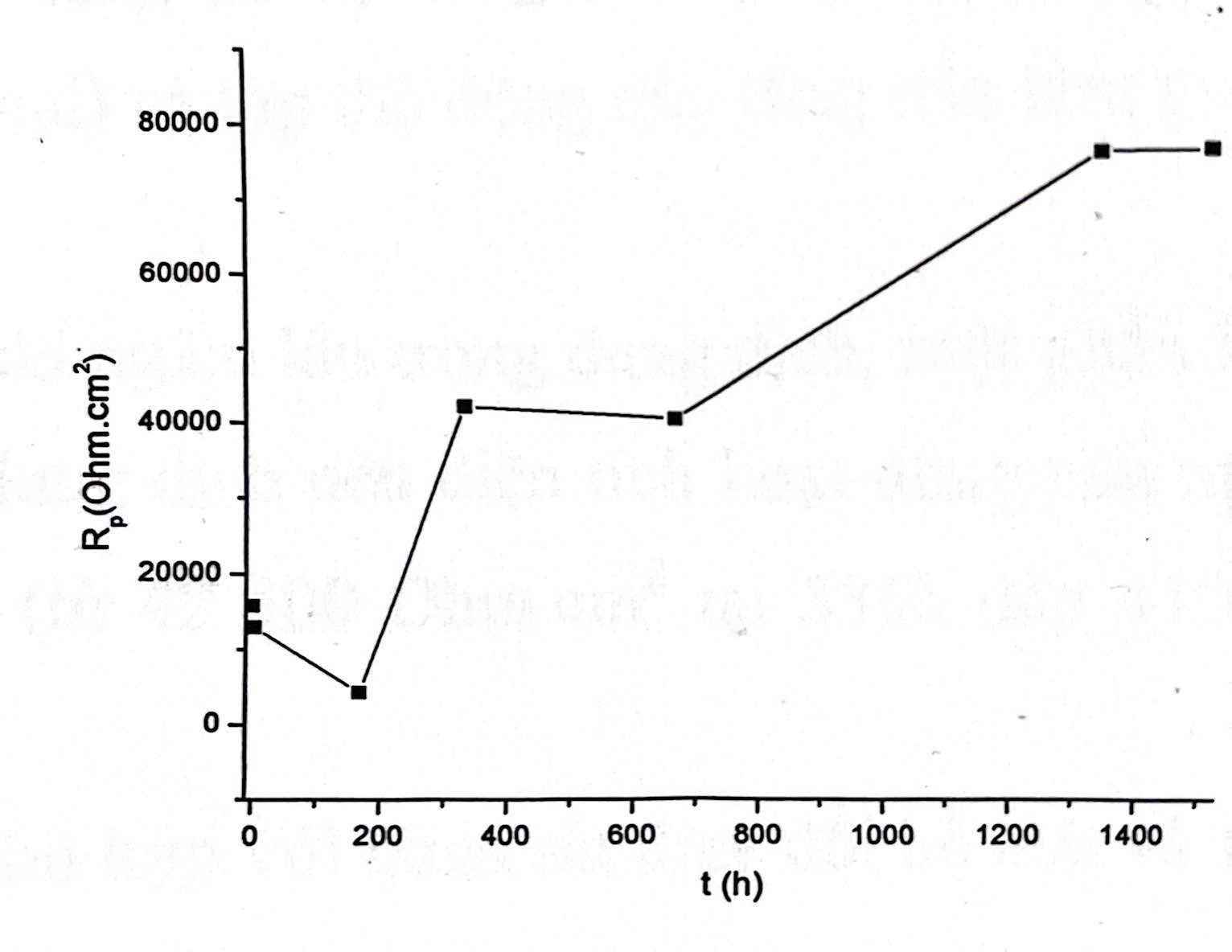
Sau 3 giờ ngâm mẫu, giá trị Ecorr có giảm nhưng không đáng kể; trong khoảng thời gian 168 - 1512 giờ ngâm mẫu, giá trị Ecorr tương đối ổn định. Kết quả đo Ecorr theo thời gian phù hợp với ảnh chụp hình ảnh bề mặt mẫu ở pH 4.
Theo thời gian, Rp nhìn chung tăng rõ rệt: Từ 168 - 1512 giờ giá trị Rp tăng 16 lần, tốc độ dòng giảm do bề mặt hình thành các lớp thụ động (oxide kim loại) và lớp thụ động này tăng dần làm giảm dòng ăn mòn. Do lớp phủ có cấu trúc xốp, khi ngâm lâu trong dung dịch, một phần lớp phủ CrNi bên trong tiếp xúc với dung dịch nên diện tích hoạt động của mẫu tăng lên, dẫn đến có thời điểm Rp giảm ít tại 336 - 672 giờ.
So sánh hình ảnh SEM lớp phủ trước và sau khi thử ăn mòn cho thấy ở pH 5 bên trong lớp phủ có nhiều lỗ xốp, các hạt lớp phủ có dạng dẹt, giữa lớp phủ và nền thép có lớp phân cách. Trên bề mặt Al xuất hiện nhôm oxide hoặc hydroxide làm giảm độ xốp của Al tạo ra trong quá trình phun phủ. Không phát hiện sự thay đổi của lớp phủ CrNi phía dưới. Như vậy, ở pH cao thì lớp phủ bị ăn mòn một chút ở bề mặt trước và sau khi hình thành các sản phẩm thụ động, nền thép không bị ảnh hưởng.
4. Kết luận
Kết quả xác định tính chất cơ lý hóa của lớp phủ cho thấy việc sử dụng lớp phủ Cr-Ni ở dưới có tác dụng tăng độ bám dính so với lớp phủ nhôm trực tiếp trên nền thép.
Nghiên cứu tính chất điện hóa, đánh giá khả năng bảo vệ chống ăn mòn của lớp phủ trong acid HCl cho thấy hệ lớp phủ bền ở pH 5, 6. Hình ảnh SEM cho thấy sự ổn định của lớp phủ ở pH 5, 6.
Dựa vào kết quả nghiên cứu trên ta thấy lớp phủ kép hợp kim CrNi và Al có thể ứng dụng trong công nghiệp, cụ thể trong điều kiện acid vô cơ công nghiệp như HCl.
TÀI LIỆU THAM KHẢO:
1. Trần Hiệp Hải (2001), Ăn mòn và bảo vệ kim loại, Nhà xuất bản Giáo dục.
2. Trịnh Xuân Sén (2000), Điện hóa học, Đại học Khoa học Tự nhiên, Đại học Quốc gia Hà Nội.
3. Wei-Min Zhao, Yong Wang, Tao Han, Kai-Yuan Wu and Jin Xue. Electrochemical evaluation of corrosion resistance of NiCrBSi coatings deposited by HVOF. Surface and Coatings Technology, Volume 183, Isue 1, 1 May 2004, Pages 118-125.
4. J.E.CHo, SY. Hwang and K.Y.Kim. Corrosion behavior of thermal sprayed WC cermet coatings having various metallic binders in strong acidic enviroment. Surface and Coatings Technology, Volume 200, Issue 8, 24 January 2006, p2653-2662.
5. Study of the Effectiveness of Corrosion Resistance Growth by Application of Layered AlN-TiO2 Coatings, Gulnaz Zh. Moldabayeva, Artem L. Kozlovskiy, Erzhan I. Kuldeyev, Askar Kh. Syzdykov and Aigul Bakesheva, Published: 22 March 2024
Development of an anti-corrosion dual coating based on chromium-nickel and aluminum alloys Nguyen Thanh Son Open Training Institute, Hanoi Architectural University Abstract: This study investigates a dual-layer Cr-Ni and Al coating designed to serve as both a barrier against corrosive agents and a protective anode for the steel substrate, even when exposed. Physicochemical analysis revealed that the Cr-Ni layer exhibits an adhesion strength of approximately 30.14 MPa on steel, surpassing that of the aluminum coating. Consequently, using Cr-Ni as an underlayer enhances adhesion compared to directly applying aluminum to steel. Electrochemical evaluations in HCl confirmed the coating’s stability at pH 5 and 6, with SEM imaging before and after corrosion testing further supporting its protective effectiveness. Keywords: acidic corrosion, corrosion, coating. |
Nguyễn Thành Sơn
Viện Đào tạo mở, Trường Đại học Kiến trúc Hà Nội