Các tác dụng mang lại khi sử dụng các loại vật liệu này bao gồm giảm nhiệt tích lũy vào vỏ lò, giảm nhiệt tổn thất qua vỏ lò, rút ngắn thời gian nung….
Bông gốm có tính cách nhiệt tốt, độ dẫn nhiệt rất thấp, chỉ bằng khoảng 1/2 đến 1/3 độ dẫn nhiệt của gạch nhẹ nên nhiệt tổn thất nhiệt qua tường lò thấp.
Do bông gốm rất nhẹ (khối lượng thể tích bằng 1/4 đến 1/5 gạch nhẹ), nhiệt tích luỹ rất thấp, chỉ chiếm khoảng 1/5 so với gạch nhẹ nên nhiệt tổn thất do tích lũy vào vỏ lò thấp. Bông gốm dạng cuộn có hiệu quả cách nhiệt cao khi được ép chặt theo tỷ lệ 1/(0.6-0.7).
Nếu lò xây bằng gạch thì tường lò phải rất dày, có thể đến 0,5m, còn nếu dùng bông gốm thì chiều dày chỉ cần 0,25m đến 0,3m. Vì vậy dùng bông gốm đã tiết kiệm được rất nhiều năng lượng do giảm tổn thất nhiệt qua vỏ lò ra môi trường xung quanh và nhiệt tích luỹ bởi vỏ lò. Khi đã tiết kiệm năng lượng thì nhiệt độ trong lò dễ dàng nâng cao và thời gian nung có thể rút ngắn lại.
+ Gạch xốp
Gạch chịu lửa xốp thường được dùng để xây ghế lò, chỗ lắp các vòi đốt và xây trên nền xe goòng. Gạch xốp có khả năng cách nhiệt tốt hơn gạch đặc nhưng nó lại dễ bị co ngót sụt lún khi chịu tải trọng ở nhiệt độ cao.
Cần chọn loại gạch xốp có chất lượng tốt (hàm lượng oxit nhôm trong gạch cao độ chịu lửa của gạch cao, độ co phụ thấp…), đặc biệt là đối với gạch xây nền xe goòng vì chúng phải chịu tải trọng lớn của khối xếp.
b. Sử dụng tấm kê, trụ đỡ khối lượng nhẹ
Tấm kê được làm bằng vật liệu chịu lửa SiC có độ chịu lửa cao và có khả năng chịu tải trọng lớn ở nhiệt độ cao. Kích thước tấm kê phổ biến là 400 x 420 mm, 490 x 520 mm, 700 x 350 mm. Tùy thuộc vào chất lượng tấm kê thì độ dày có sự thay đổi, thường chất lượng càng tốt thì tấm kê càng mỏng.
Để giảm khối lượng tấm kê mang vào lò, nhiều doanh nghiệp đã cung cấp ra thị trường các loại tấm kê mỏng, biên dạng bố trí theo hình dạng và cách xếp sản phẩm, thậm chí khoét lỗ để giảm khối lượng.
c. Giảm nhiệt độ nung sản phẩm, rút ngắn chu kỳ nung
Nắm vững các quá trình hóa lý xảy ra trong sản phẩm khi nung để thiết lập được một chế độ nung thích hợp nhất, qua đó rút ngắn được thời gian nung, nâng cao được chất lượng sản phẩm. Đường cong nung sứ dân dụng, mỹ nghệ bao gồm các giai đoạn như sơ đồ dưới đây:
d. Tận dụng nhiệt khói thải khi nung và không khí nóng khi làm nguội lò
Một trong những giải pháp có thể tận dụng tốt nhiệt thải của lò nung là việc kết nối của cụm 4 lò gián đoạn, vận hành nối tiếp nhau. Nhiệt khói thải của lò đang nung sẽ được đưa sang sấy nóng cho lò nung kế tiếp. Nhiệt không khí nóng của lò đang làm nguội sẽ được cấp vào lò đang nung để đốt cháy nhiên liệu. Một lò còn lại trong cụm lò sẽ thực hiện việc xếp dỡ sản phẩm.
Một giải pháp đơn giản và dễ thực hiện hơn đó là thiết kế 2 bộ xe goòng cho 1 lò nung. Khi 1 bộ xe goòng đang được nung trong lò thì bộ xe goòng chờ bên ngoài thực hiện việc xếp, dỡ sản phẩm. Khi nhiệt độ trong lò nguội xuống khoảng 200oC thì có thể kéo xe goòng trong lò ra và đẩy goòng chờ vào lò, khi đó nhiệt tích lũy trong vỏ lò sẽ truyền cho xe goòng mới. Như vậy hoàn toàn không tiêu tốn nhiên liệu cho việc nâng nhiệt độ toàn bộ lò lên khoảng 200oC.
Trong quá trình nung có thể tận dụng nhiệt từ khói thải để đưa sang buồng sấy để sấy khô mộc và khuôn. Quá trình rút khí từ ống khói đưa sang buồng sấy cần đảm bảo không ảnh hưởng đến chế độ cháy trong lò. Nhiệt sấy cũng cần được kiểm soát để đảm bảo kỹ thuật cho quá trình sấy. Nhiệt sấy khuôn không được vượt quá 70oC. Trường hợp chưa kịp đủ hàng cho mẻ nung tiếp theo thì có thể sử dụng lò lúc này như 1 buồng sấy để sấy khô sản phẩm mộc. Khi mộc được sấy khô tốt thì sẽ rút ngắn được thời gian dấm sấy.
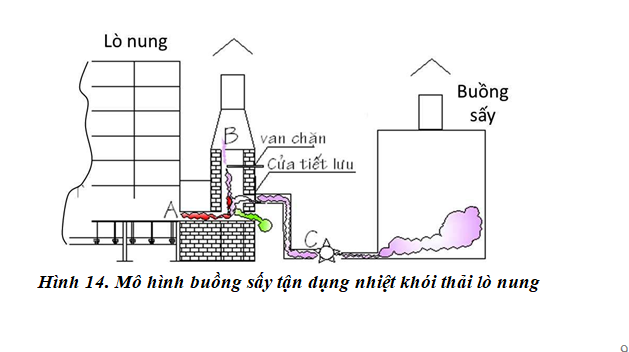
e. Nâng cao dung tích lò
Nhìn chung, dung tích lò càng lớn thì nhiệt tiêu hao riêng càng giảm. Vì vậy, các doanh nghiệp sản xuất cần cân nhắc lựa chọn dung tích lò phù hợp với năng lực sản xuất, hạn chế việc sử dụng đơn lẻ nhiều lò dung tích nhỏ.
Hiện nay, lò con thoi lửa đảo vận hành theo nguyên lý sức hút tự nhiên đã được cải tiến và nâng cao dung tích lên đến trên 100 m3 mà vẫn đảm bảo được chất lượng đồng đều cho sản phẩm nung.
Với lò dung tích lớn như vậy, thay vì xe goòng di chuyển ra vào lò như dạng thông thường thì ở đây xe goòng được thiết kế cố định, vỏ lò được thiết kế chuyển động tịnh tiến trượt ra khỏi nền lò khi thực hiện việc xếp dỡ.
Lò dung tích lớn phải được tính toán kỹ thuật chi tiết để đảm bảo độ cứng vững, chịu sự giãn nở nhiệt từ quá trình nung. Lò cũng phải đảm bảo tính đồng đều trường nhiệt độ tại các vị trí khác nhau trong lò để sản phẩm được chín đều.
Hình 15. Lò con thoi dung tích lớn với thiết kế vò lò di động
Một vài đề xuất đối với doanh nghiệp sản xuất gốm sứ
Trên cơ sở phân tích những vấn đề liên quan đến công nghệ và thiết bị sản xuất gốm sứ, có thể đề xuất một số vấn đề giúp các doanh nghiệp tiết giảm được chi phí năng lượng trong sản xuất gốm sứ, cụ thể như sau:
- Khi đầu tư lò nung mới, nên lựa chọn lò nung với kết cấu vỏ lò bằng bông gốm, ép thành tấm panen, lựa chọn nhà cung cấp lò có uy tín.
- Cân đối tài chính, năng lực sản xuất để đầu tư lò có dung tích thích hợp. Nên chọn lò dung tích lớn 4-5 ngày nung 1 chuyến thay vì dùng lò dung tích nhỏ 2-3 ngày nung 1 chuyến.
- Nên lựa chọn hệ tấm kê, trụ đỡ chất lượng cao, mỏng, nhẹ. Chi phí đầu tư ban đầu cao sẽ nhanh chóng được bù lại bằng lượng năng lượng tiết kiệm và bằng chính tuổi thọ của tấm kê, trụ đỡ.
- Nên đầu tư buồng sấy mộc tận dụng nhiệt khói thải lò nung để sấy khô triệt để mộc, rút ngắn thời gian dấm sấy khi nung.
- Nếu có thể, hãy kết hợp thành cụm lò nung để tận dụng tối đa nhiệt thải của các lò.
TS. Nguyễn Thành Đông - Đại học Bách khoa Hà Nội
(Nguồn: Tạp chí Công Thương)